Hobart Brothers Develops Revolutionary New Metal-Cored Wire for Robotic Welding |
|
 |
TROY, OH - Hobart Brothers has developed a revolutionary new metal-cored welding wire designed to maximize performance and increase productivity on high-volume robotic welding applications, especially those for heavy equipment manufacturing. The new Matrix™ wire from the company's Tri-Mark® brand is a first of its kind in the industry-a proprietarily manufactured product formulated specifically to provide uncompromised arc starting and wire feeding consistency. The exacting nature of this proprietary manufacturing process ensures that Matrix performs the very same-time and again—regardless of the application. Matrix's reliable arc starting and excellent wire feedability are the result of a Hobart Brothers' exclusive technology. This special technology has also been shown to extend the life of robotic gun liners and to eliminate buildup at the drive rolls. Each of these features reduces downtime for maintenance and post-weld activities, and ensures greater overall welding productivity. |
• For more information please click here |
|
MORE NEWS |
|
 |
Mitsubishi Makes a Splash with Precision Waterjet for EDM |
|
Miller Electric Mfg Introduces New Spoolmate 200 Spool Gun Optimizes MIG Aluminum Welding in Light Fabrication, Repair Applications |
Wood Dale, IL - Mitsubishi introduces the first waterjet line designed specifically to work hand-in-hand with EDM technology. The Waterjet line brings speed and flexibility to EDM shops, while maintaining the level of reliability and accuracy required in EDM manufacturing. Mitsubishi experts have played an active role in the Waterjet machines' design, making sure they're engineered specifically to work with EDM technology. Mitsubishi engineers are constantly delivering ways to increase efficiencies and boost productivity. The machine's speed is ideal for reducing production times attached to roughing and bulk material removal before finishing on EDM. For example, a time study showed a 28% time savings on materials roughed with Waterjet versus an EDM machine. The Waterjet series is available in three different models to best fit every shop's needs. These include the 2-3 axis Classica, 4-axis Suprema, and 5-axis Evolution. The machines feature stainless steel tanks for easier maintenance and cleaner cutting conditions. A solid base construction and custom-made table for accepting tooling systems allows Waterjet and EDM to easily work together. |
|
Appleton, WI - Miller Electric Mfg. Co. introduces its new Spoolmate™ 200 spool gun, designed as a cost-effective option for light- to medium-duty aluminum fabrication and repair work. Improving productivity and increasing the user's work envelope, the Spoolmate 200 features handle-based wire feed speed adjustment and a 20-foot power cable, allowing operators to conveniently adjust their wire parameters while working at a distance from their power source. The Spoolmate 200 also offers curved and extended barrel options, ideal for sign makers, boat fabricators and others who frequently contend with tight and difficult-to-reach joint configurations. Also improving joint access, the shielding gas hose is bundled within the power cable assembly. For higher-amperage aluminum welding, an optional heavy-duty barrel is also available. The Spoolmate 200 plugs directly into the Millermatic® 212 w/Auto-Set™ and the Millermatic® 252, both of which feature spool gun direct connections so that users do not need to remove their steel MIG gun to install their aluminum spool gun. For added convenience, the Spoolmate 200 contains a built-in gas solenoid, allowing users to switch processes without changing gas cylinders. |
• For more information please click here |
|
• For more information please click here |
|
New Mate LongLife Slitting Tool System For Trumpf Style Punch Presses Features M4PM Tool Steel For Long Life Operation |
|
Amada Introduces Faster & More Cost-effective Turret Punch Press Series |
Anoka, MN - Mate Precision Tooling announces introduction of its new Slitting Tool System For Trumpf style punch presses featuring M4PM tool steel. Fully OEM compatible, Mate LongLife is the market's only punch press tool slitting system utilizing M4PM tool steel. This tool steel provides the highest tool performance with superior wear resistance and increased toughness, resulting in higher quality punched parts and longer tool life. "Made of M4PM tool steel, Mate LongLife is designed to replace conventional punches and dies, thereby delivering exceptional value to the fabricating process," reports John Galich, Mate marketing manager. "It provides fabricators with another option to improve productivity and profitability." M4PM is a proprietary metallurgical steel composition that utilizes a special particle metallurgical manufacturing process and triple temper heat treatment resulting in the world's finest tool steel for use in punching tools, reports Galich. |
|
Buena Park, CA - To help shops of all sizes address market demands for punching that is faster and more cost-effective, Amada introduces the AC 255/2510NT series of turret punch presses. The ram of this punching system is driven by an AC servo motor, which enables fabricators to greatly increase punching speeds. Combined with innovative tooling designs, it performs functions that would normally have to be done as secondary operations. Some of these include: high-speed contouring, burr-free slotting, high-speed marking, and complex forming that would normally have to be done by press brake. The AC-NT series provides significantly faster punching speeds than mechanical turrets while eliminating the need for a hydraulic power supply and its attendant chiller. Other cost efficiencies are made possible by design enhancements, such as the machine's ability to operate using half the electrical power of comparable competitive units. As an added benefit, the AC-NT series has been designed to fit in a smaller footprint, this in response to user requests for more floorplan-friendly machines. |
• For more information please click here |
|
• For more information please click here |
|
LVD Introduces Automation-Ready Flying Optics Laser Cutting Systems for Fast, Efficient Sheet Metal Processing |
|
CWP Line Boosts Productivity for Lawn & Garden Equipment Manufacturer |
Gullegem, Belgium - LVD Company n.v. introduces Sirius, an automation-ready flying optics laser cutting system. Sirius is designed to provide efficient processing of parts at optimal speeds and accelerations to suit the part geometry, offering reliable cutting performance at an affordable price-performance ratio. Sirius is offered in a standard and a Plus model. The Sirius Plus is optimized with additional features and automation capabilities. Sirius provides quick and precise positioning and consistently accurate laser processing. The combination of a dynamic machine with an excellent laser beam quality allows high-speed laser cutting. Quick positioning is achieved with axis speeds up to 120 m/min. Sirius is designed with a modular construction, permitting the user to select the configuration that works best for the application and budget. As a standard unit, the laser cutting system features 3 m by 1.5 m integrated shuttle tables, which maximize uptime by allowing one table to be loaded while the machine is cutting on the other table. Table change time is a mere 25 seconds. |
|
Clinton, ME - As a leading manufacturer of premium quality lawn and garden tractors, Simplicity Manufacturing, Inc., uses a lot of steel. So when they needed a new coil handling system to increase their processing capability, they installed a 12" wide Cooper Weymouth Petersen (CWP) coil handling system with the ability to handle material up to .250" thick. equipment selection process," says John Wolfe, fabrication supervisor at Simplicity. "The CWP system we eventually selected provides both of these benefits." The coil handling system uses CWP's Model SMX12H Servomax feed, proving full-width capacity through gear-driven, four-inch diameter feed rolls. The feed was equipped with an automated, powered passline adjustment function to speed up passline adjustments when changing tooling over. To further increase changeover speed, pushbutton clamping/unclamping of the feed unit to the press was also included. At Wolfe's request, a CWP Model 4RD double-stock reel was added to provide an easier method of partial coil changeover. At 8,000-lb capacity per spindle, the reel is equipped with hydraulic expansion, inching drive and hold-down arms with powered rider roll. Each function is independently operated for each spindle. |
• For more information please click here |
|
• For more information please click here |
|
ESAB Introduces New Rollerbeds for Workpiece Handling |
|
Veridiam Medical Introduces Advanced Spin Welding Capabilities for Specialized Joining of Plastics to Metals |
Mississauga, ON - ESAB Welding & Cutting Products is pleased to announce the addition of new conventional and self-aligning rollerbeds to its line of automated handling equipment products. These new rollerbeds are available in North America and replace ESAB's previous turning roll products. ESAB Canada will stock the new rollerbeds at their Mississauga, Ontario, and Edmonton, Alberta, warehouse facilities to ensure on-time delivery for North American customers. These durable rollerbeds are grit-blasted with a polyurethane finish coating to endure abrasive environments. They also feature solid-state inverter technology for precise speed control to ensure welding accuracy. The rollerbeds are available in a variety of sizes and driver/idler rail bogie versions for a broad scope of applications. Depending on the project, fabricators can choose from conventional rollerbeds with load capacities from 2.5 - 60 tons or self-aligning rollerbeds with load capacities from 2.5 - 50 tons. These workpiece handling solutions are ideal for wind tower fabrication, offshore and shipyard, pressure vessels and pipelines. |
|
San Diego, CA - VERIDIAM MEDICAL, a leading provider of assemblies, machined parts and metal tubular components specifically engineered to meet the demanding requirements of medical device manufacturers, introduces new Spin Welding capabilities to its array of specialized manufacturing operations. The new Spin Welder allows plastic components to be quickly, cleanly, and permanently attached to metal assemblies. The addition of this machine allows Veridiam Medical to manage complex projects that require both metal manufacturing and plastic attachment, saving both time and money for their customers. Prior to the introduction of this new capability, Veridiam Medical would construct complex metal components, then outsource these to outside vendors for the assembly of the plastic portion. Plastics vendors, unfamiliar with medical device development, can include unnecessary features in their parts. The Spin Welder allows Veridiam Medical to integrate the manufacture of components entirely in-house, employing their expert knowledge of medical device design and development. |
• For more information please click here |
|
• For more information please click here |
|
Dytran Introduces New Family of Impulse Hammers |
|
Sandvik Coramant: Developments Pave the Way to Higher Performance in Milling |
Chatsworth, CA - Dytran Instruments, Inc. now offers impulse hammers with TEDS capability. The 5800BT Series is a new family of impulse hammers (similar to the 5800B Series) which feature acceleration compensation and IEEE 1451.4 TEDS. With a head weight of 100 grams, they are available in five ranges, between 50 LbF and 1,000 LbF. The 5800BT Series utilize an exclusive acceleration compensated quartz force sensor to ensure that hammer self-resonances do not produce spurious "bumps" in the hammer output spectrum. The high rigidity of the force sensor combined with acceleration compensation produces a clean, smooth output signal which is an exact representation of the forcing function, both in amplitude and phase. Dytran's piezoelectric impulse hammers of a head assembly containing a force sensor and a handle with a rubber grip, as well as interchangeable head extenders and several different impact tips (steel, aluminum and soft plastic). Permanently mounted to the front surface of the hammer head is an IEPE force sensor, with electrical connections conveniently routed through head and handle, and terminating to a BNC connector located at the end of the handle. This streamlined design concept was pioneered by Dytran and has since become the industry standard. |
|
Fair Lawn, NJ - CoroMill® 490, the versatile face and shoulder mill is designed to cut tool costs and inventories and can now be applied in stainless steel machining. Advanced grades GC2030, GC2040 and GC1030 with new geometry types are introduced in a complement to the existing assortment for steel, hardened steel and cast iron machining. The inserts have sharp edge lines and produce cuts with burr-free profiles, making CoroMill 490 the first mill to produce a true 90 degree square shoulder cut without sharp steps. This advanced tooling solution offers higher precision and tighter component tolerances, as smoother surfaces are produced with no discernable cusp. CoroMill 345, the new generation 45° face mill designed for high performance in steel and stainless steel, now benefits from a full insert range for cast-iron and a new mirror-finishing geometry for steel. Cylindrical and weldon-shank cutters are also released. This highly efficient face mill combines top performance with light-cutting action. Inserts with 8-cutting edges provide economy and make CoroMill 345 suitable for demanding roughing to mirror-finishing applications. It optimizes processes in a variety of machine tools, with cutters available over a diameter range of 40-250 mm. |
• For more information please click here |
|
• For more information please click here |
|
Milwaukee Electric Tool Corp Introduces of their First Offering in the 3/8" Tradesman Drill Category |
|
The New RIDGID Endura-Clear Thread Cutting Oil Maximizes Wear Resistance Increasing Die Life |
Milwaukee - Electric Tool Corporation adds to it legendary line of corded drills with the introduction of their first offering in the 3/8" tradesman drill category. The 0240-20 delivers on Milwaukee's heritage of durability and performance in corded drills with an all metal jampot gear case, powerful 8 Amp motor and best in class drill speed. "Competitive 3/8" Drills in this price range typically utilize a clamshell plastic housing design," says Melissa Marineau, Group Product Manager. "The 0240-20's all-metal gear case and jampot design adds rigidity and greater support for the gears, resulting in increased performance and greater durability over the life of the tool." Ideal for small diameter drilling and fastening applications, the new MILWAUKEE® 3/8" drill delivers performance with a powerful 8 Amp motor and 0-2,800RPM variable speed, which results in drilling holes up to 85% faster. Complete with an all metal keyless chuck and soft-grip main handle, the 0240-20 is easy to use and withstands job site abuse in professional applications. |
|
Cleveland, OH - Endura-Clear thread cutting oil, the newest addition in the RIDGID® thread cutting oil product line, maximizes wear resistance, increases die life, decreases operating costs and is CPVC compatible. "Endura-Clear thread oil is a great addition to our product line because it extends the life of dies up to 60 percent, while significantly reducing threading machine operating costs up to 30 percent over the RIDGID Nu-Clear oil," said Larry Feskanich, product manager, RIDGID. The formula has been tested to assure chemical compatibility with FlowGuard Gold®, BlazeMaster®, and Corzan® CPVC pipe and fittings and has been added to the FGG/BM/CZ™ System Compatible Program. Endura-Clear thread oil contains an anti-mist formulation to inhibit inhalation and decrease mess. It maintains a workable viscosity for cold weather threading to negative 20 degrees Fahrenheit and is available in a one-gallon size. |
• For more information please click here |
|
• For more information please click here |
|
Methods Introduces World's First Twin ATC B-Axis Multitasking Turn/Mill System |
|
Haas Introduces New Drill and Tap Machine Features Milling Capability |
Sudbury, MA - Today, Methods Machine Tools Inc., a leading supplier of innovative precision machine tools, has introduced the Nakamura-Tome Super NTMX Multitasking Turn / Mill Machining Center. The Super NTMX is the world's first system to offer dual 24-tool ATC magazines, a unique design to simplify complex multitasking machining. Full 5-axis milling capability via a Fanuc 31iA5 Control provides high precision and accuracy for manufacturing complex contoured components, including medical, aerospace and more, in large or small volume production. "With the introduction of the cost-effective Super NTMX, today's manufacturers have a simple, high performance 5-axis multitasking solution in a system which is very easy-to-operate," said Mr. Richard Parenteau, Director of Application Development at Methods Machine Tools Inc. "In addition, it offers shops a great deal of flexibility due to its 2 ATC magazines and programming, process versatility." |
|
The new DT-1 from Haas Automation, Inc., is a compact, high-speed drill and tap machine with full milling capabilities. The machine features a generous 20" x 16" x 15.5" work cube and 26" x 15" T-slot table, while maintaining a very small footprint. A powerful BT-30 taper spindle spins to 15,000 rpm, and allows tapping at speeds to 5000 rpm. The spindle is coupled directly to the motor for smooth, quiet operation and extreme thermal stability. A 15-hp vector drive system provides 46 ft-lb (peak) of cutting torque for milling and boring operations. The DT-1 is equipped with a high-speed, 20-pocket, servo-driven tool changer that swaps tools in 0.8 seconds. High-speed 2400 ipm rapids combine with 1G acceleration rates to shorten cycle times and reduce non-cutting time. The maximum cutting feedrate is 1200 ipm. For efficient chip removal, the DT-1 features steeply sloped internal sheet metal. Optional twin chip augers transport chips to exit at the rear of the machine. A 45-gallon flood coolant system is standard, with options for a programmable coolant nozzle and high-pressure through-spindle coolant systems. |
• For more information please click here |
|
• For more information please click here |
|
Fab Masters: One Stop Machining, Fabrication and Assembly |
|
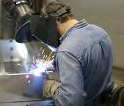 |
Fab Masters Company is a progressive independent manufacturer of custom aluminum machined and fabricated parts. Our goal; to help you control your costs. Our one-stop shop, one purchase order; can supply you with, aluminum extrusions, precision cutting, CNC machining, certified welding, fabrication, finishing, lite assembly, and shipping to you or your customers. Fab Masters is a major provider of machining services to the extrusion industry in the Midwest, is ISO 9001:2000 certified, in a 102,000 square foot facility located centrally between Chicago and Detroit. Fab Masters Co. has been serving the aluminum extrusion industry for over 25 years with exceptional customer service and quality assurance and is willing to accept new challenges and handle a wide array of fabrication needs. FMC supplies services from raw extrusion acquisition thru delivery to your door. |
• For more information please click here |
|
OTHER NEWS |
|
 |
|
|